About Us
About Us
PRIME ENERGY USA is leading the digital transformation of technologies in all oil refinery processes and business operations, which signifies a revolutionary shift from traditional methodologies, embracing cutting-edge technologies to streamline processes and tackle environmental and sustainability challenges.
Incorporating advanced process control systems, artificial intelligence, and machine learning marks a watershed moment for refineries using Prime Energy’s proven application specific software solutions.
PRIME ENERGY USA Is Navigating all of the Challenges in Refinery Digitalization and OPTIMIZATION.
How Are Oil Refineries Transforming Operations With Digital Innovations For Sustainability?
Design Startup and Commissioning of Non-Linear Real-Time SME ON All refinery and gas process units. Advance Process Control Systems yearly savings calculation on using all of ACSC real time physical property and Simulation Models methodologies to support capacity modeling enhancements, including improved forecasting and optimization techniques and integration of process unit systems. We try building as much electrical and software redundancy as possible in all of our projects.
Experience in SCADA and DCS support and troubleshooting problems in all aspects, and specifically data quality integration issues including:
Data quality and consistency issues for the near real-time updating of RTU/PLC data OSI-PI-System performance optimization.
Digital transformation in oil refinery operations signifies a revolutionary shift from traditional methodologies, embracing cutting-edge technologies to streamline processes and tackle environmental challenges. The incorporation of advanced process control systems, artificial intelligence, and machine learning marks a watershed moment for refineries.
These innovations usher in a new era, empowering refineries to synchronize with sustainability objectives, elevate operational efficiency, and adhere to rigorous regulatory benchmarks.
This transformative journey is rooted in the industry’s unwavering dedication to diminishing its environmental impact and nurturing enduring environmental responsibility. By deploying these technologies, refineries not only optimize their operations but also contribute significantly to the broader commitment to a greener, more sustainable future in the oil and gas sector.
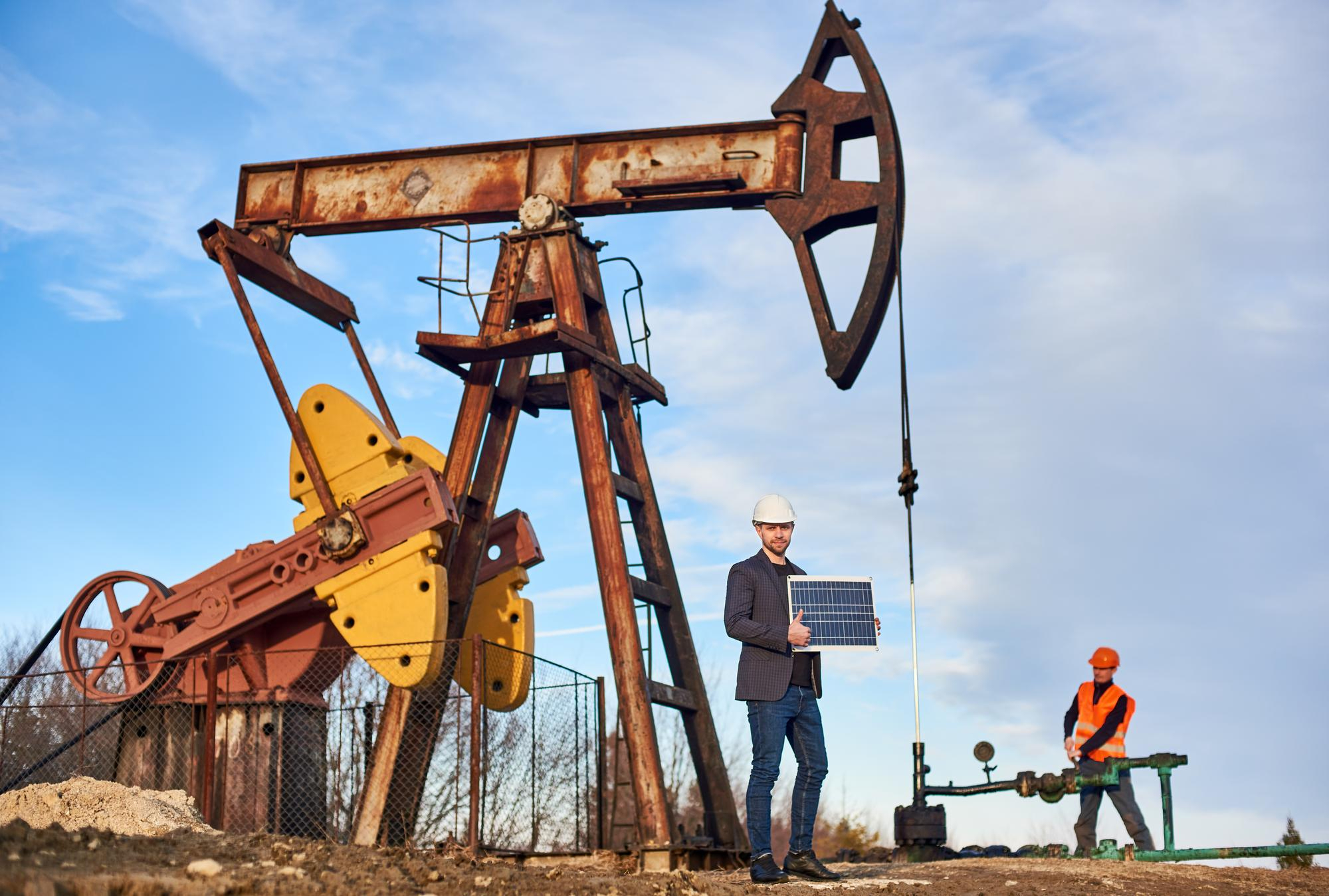
Building Real-Time Manufacturing Visibility Platform: Using common manufacturing visualization platforms, you will be developing and building an enterprise-wide visualization platform to support troubleshooting and decision making.
Driving Operational Improvement Projects: Focusing on sustainable gains in reliability, quality, safety, cost, and delivery using methodologies like Nestle Continuous Excellence, TPM, and LEAN fundamentals. Assist functions/manufacturing groups in identifying opportunities, collecting, analyzing business requirements, and performing data analysis to address business needs. Cross-Functional Collaboration: Working with division, factory, and internal partners to achieve business outcomes.
Navigating Challenges in Refinery Digitalization
Two significant challenges in implementing digital transformation in oil refinery operations are legacy infrastructure and resistance to change. Legacy systems may lack compatibility with advanced technologies, requiring extensive upgrades and investments. Resistance to change from established workflows and personnel can impede the smooth integration of digital solutions. Addressing these challenges demands a delicate balance between innovation and practicality.
Upgrading existing infrastructure while ensuring minimal disruption to daily operations is a complex task. Overcoming resistance through comprehensive training and change management is equally vital. Navigating these challenges is pivotal for refineries to fully harness the benefits of digital transformation and advance sustainability in their operations.
How Can Oil Refineries Successfully Embrace Digital Transformation for Sustainability?
Oil refineries can surmount digital transformation challenges through strategic solutions. Creating a well-defined integration roadmap, incorporating phased implementation and rigorous risk assessments, proves effective in mitigating potential disruptions. Collaboration with technology providers, like IBM or Siemens, and engaging industry experts ensures access to cutting-edge solutions, addressing cybersecurity concerns. Companies such as Chevron and ExxonMobil have embraced advanced technologies for efficiency gains.
Investing in employee training and change management programs, exemplified by Shell’s workforce development initiatives, fosters an innovative culture. Clear communication channels, as demonstrated by BP’s transparent approach, coupled with stakeholder engagement mechanisms, facilitate a smooth transition. Proactive measures like these empower oil refineries to optimize processes, reduce emissions, and actively contribute to the industry’s sustainability objectives.
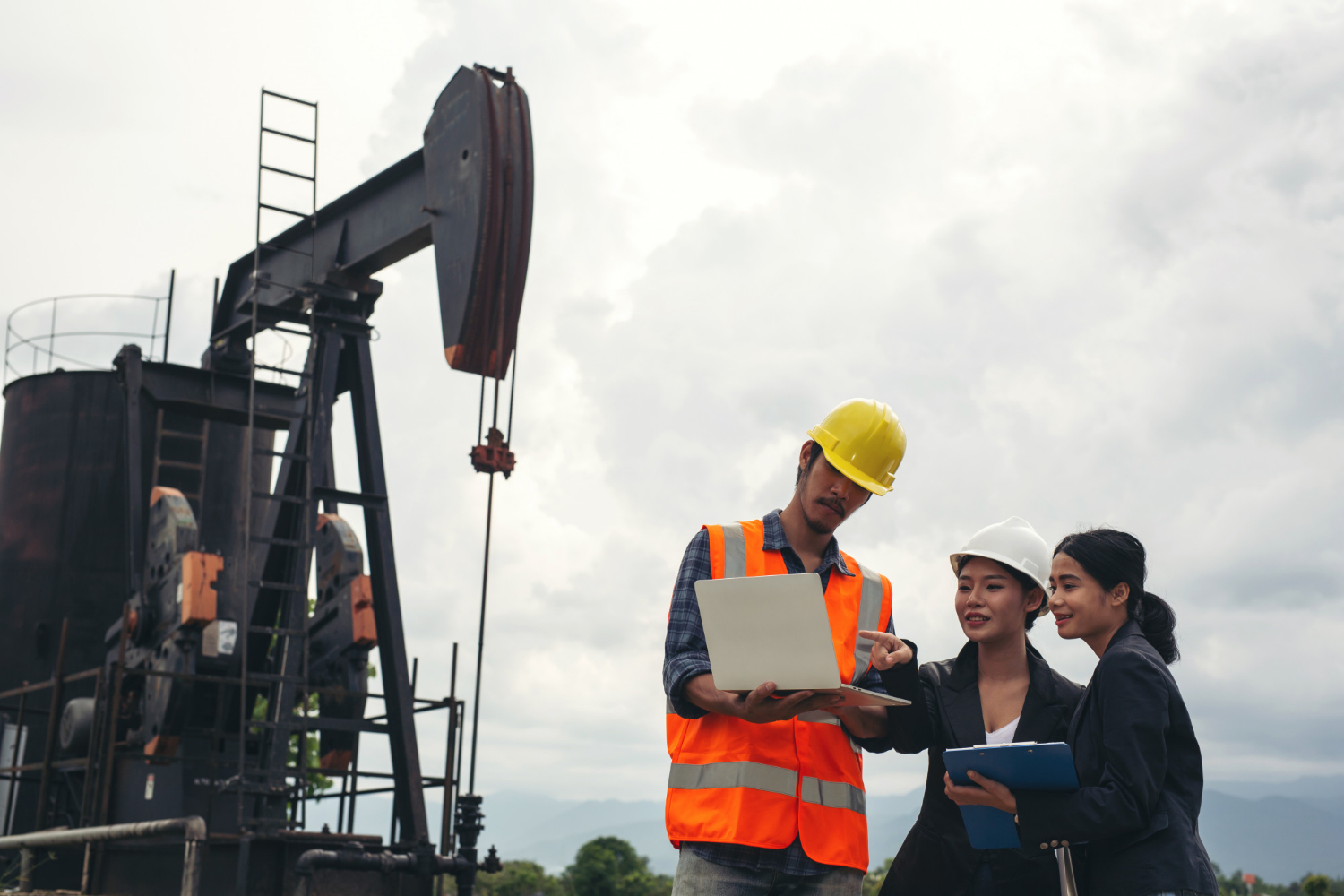
Refiners worldwide are diversifying production from fuels toward petrochemicals.
This is due to expected future declines in fuels demand, combined with significant global growth for petrochemicals. New grassroots complexes around the world are being built to include petrochemicals production to meet this demand and to achieve higher margins.
In the U.S., gasoline and diesel demand are forecasted to decline. In 2035, gasoline demand is expected to be about 15 percent lower than in 2018. Similarly, diesel demand will be down 6 percent. This decline is due to several factors including continued technology improvements in vehicle energy efficiency, renewables substitution, autonomous vehicles, shared and connected vehicles and changing demographic behaviors.
As both gasoline and diesel decline, the refiner’s ability to maintain profitability requires modernization and diversification. Additionally, U.S. refiners currently export off-specification gasoline to countries where specifications are less strict. Expanded refining capacity and stricter fuel specification changes in these regions will reduce demand for this gasoline. U.S. refiners therefore need to consider alternatives to fuels production in light of decreasing domestic and export demand.
There also is a scenario where refiners would produce higher octane gasoline than is produced today. In a future where high compression ratio engines are needed to meet CAFE fuel efficiency standards, refiners will need a way to produce greater amounts of higher-octane gasoline.
Through petrochemical integration, refiners can maintain crude capacity and produce higher value petrochemicals while co-producing on-specification gasoline at a reduced rate. Petrochemical integration avenues are available to increase the upgrade value of crude.
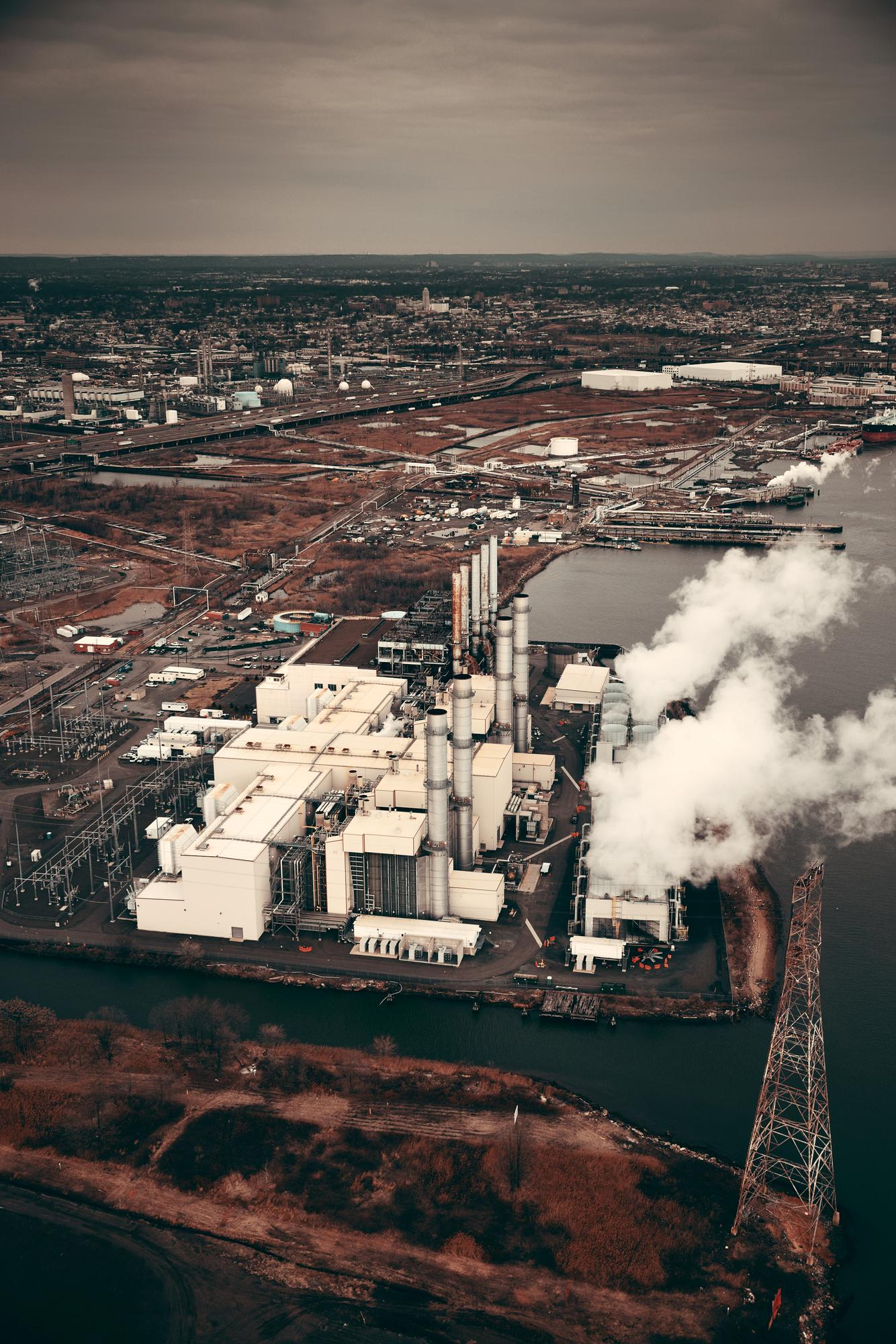
Refiners already have captured at least one third (or $15 per barrel) of the available crude upgrade value by producing fuels. This business model has served refiners well for many decades, but now there is an opportunity to further increase this upgrade value by an additional $30 per barrel. Diversifying into petrochemicals will enable refiners to remain competitive, while low-cost energy and LPG feedstock will maximize value.
This paper presents a stepwise petrochemical integration strategy developed for a typical FCC-based U.S. refinery focused on making Tier 3-compliant fuels. The investment steps build on each other, and may be implemented sequentially, depending on market conditions and the availability of capital. It also presents examples highlighting the importance of scrutinizing invitation to bid configurations to determine if higher value solutions are possible.
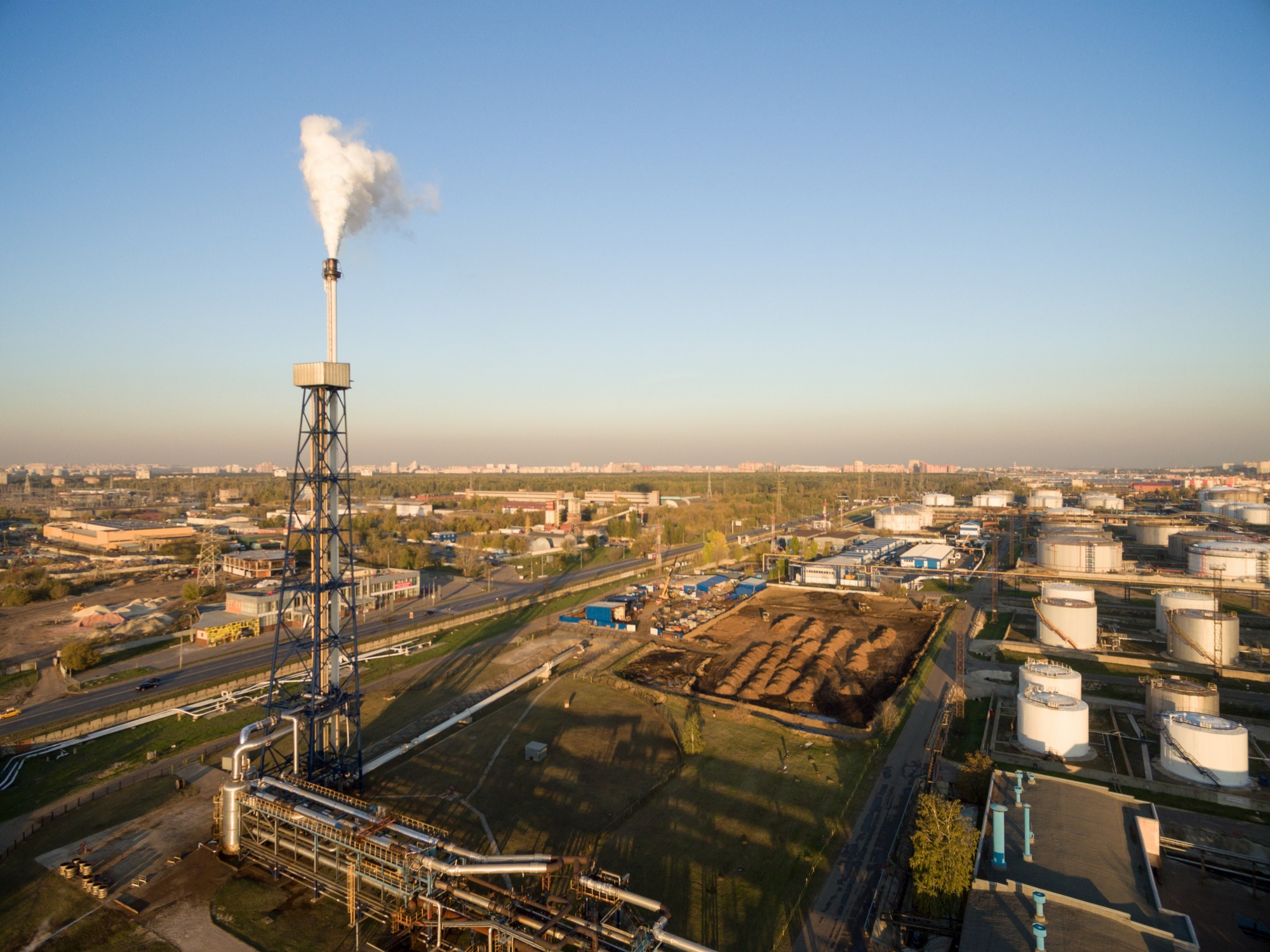
Petrochemical integration is a complex and capital intensive problem, requiring a strategy that definitively quantifies value at each step. The key is optimization rather than maximization. Optimization means better molecule management and improved configurations.
Prime Energy along with it’s software technology partner’s and world wide consultants are helping refiners develop project and investment plans for the integration and by selecting the proper catalysts, adsorbents and advanced process control echnologies software applications ,and integrating them for maximum efficiency and flexibility.